Rust Prevention and Corrosion Control: The Role of Industrial Painting
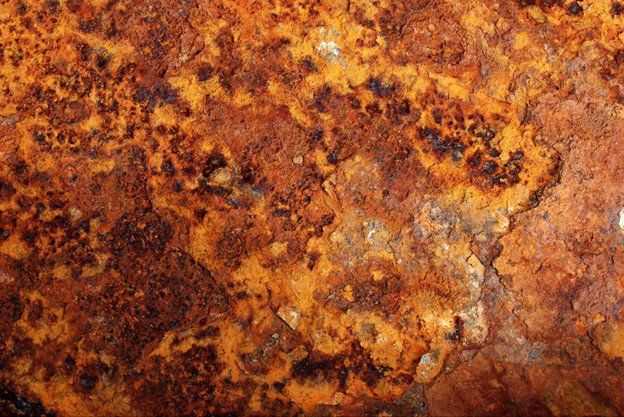
In the world of industry, rust and corrosion are formidable adversaries, posing threats to the integrity, safety, and functionality of vital structures and equipment. Fortunately, industrial painting emerges as a frontline defense against these destructive forces. In this article, we will delve into the critical role of industrial painting in rust prevention and corrosion control, safeguarding the durability and reliability of industrial assets.
Understanding the Impact of Rust and Corrosion:
Rust and corrosion are chemical processes that gradually deteriorate metal surfaces and structures over time. Here's why they are a significant concern in the industrial landscape:
- Structural Integrity: Corrosion can compromise the structural integrity of industrial equipment, pipelines, bridges, and other vital infrastructure. Weakening of metal structures can lead to accidents, failures, and costly repairs.
- Safety Hazards: Corroded equipment and structures pose safety hazards to workers and the environment. Catastrophic failures can result in injuries, environmental contamination, and financial liabilities.
- Efficiency Loss: Rust and corrosion can decrease the efficiency and operational lifespan of industrial assets. Reduced efficiency leads to increased energy consumption, maintenance costs, and downtime.
- Financial Impact: The economic impact of corrosion is significant. Industries worldwide spend billions of dollars annually on corrosion-related maintenance, repairs, and replacements.
The Role of Industrial Painting in Rust Prevention and Corrosion Control: Industrial painting is a proactive strategy that provides a protective shield against rust and corrosion, offering several benefits:
1. Protective Coatings:- Industrial painting involves the application of specialized coatings designed to act as a barrier between metal surfaces and corrosive elements. These coatings prevent moisture and oxygen from reaching the metal, slowing down or halting the corrosion process.
- Prior to painting, thorough surface preparation is essential. This process includes cleaning, removing rust and existing coatings, and properly priming surfaces. Proper surface preparation ensures the adhesion and effectiveness of protective coatings.
- Industrial painting contractors use coatings and paints specifically formulated for their anti-corrosion properties. These coatings are designed to withstand harsh industrial environments, including exposure to chemicals, saltwater, and extreme temperatures.
- Industrial paint coatings are engineered to be durable and long-lasting. They provide extended protection against rust and corrosion, reducing the frequency of maintenance and reapplication.
- Industrial painting not only protects but also enhances the appearance of equipment and structures. A well-maintained and aesthetically pleasing industrial environment can boost morale and pride among employees.
- Many industrial painting solutions are now formulated with environmentally friendly, low-VOC (Volatile Organic Compounds) options. These coatings provide effective protection while minimizing environmental impact.
- The investment in industrial painting pays off in the form of reduced maintenance costs, extended asset lifespan, and fewer repair and replacement expenses.
- In many industries, there are regulations and standards in place that mandate corrosion prevention measures. Industrial painting helps facilities remain compliant with these requirements.
In conclusion, industrial painting is a powerful tool in the fight against rust and corrosion, preserving the longevity and reliability of industrial assets. By proactively applying protective coatings and employing proper surface preparation techniques, industries can reduce the financial burden and safety risks associated with corrosion-related issues. Industrial painting is not only about aesthetics but also about safeguarding the infrastructure and assets that drive industrial operations forward.